How Suppressors Are Made: Inside SilencerCo’s Process
Stephanie Kimmell
Suppressors are built first and foremost to save your hearing—but don’t mistake them for simple noise-dampeners. They’re carefully engineered devices that represent the intersection of science, craftsmanship, and modern manufacturing. Today’s suppressors are trusted by hunters, duty professionals, precision shooters, and weekend plinkers alike.
But how are they made? What happens between the moment raw metal arrives at a facility and the moment a serialized suppressor ships to a dealer’s shelf?
To find out, I went inside SilencerCo’s Utah manufacturing facility—a state-of-the-art operation where innovation meets precision at every stage. I met the engineers, machinists, and technicians responsible for producing some of the most respected suppressors on the market.
Here’s what I saw—and how it all comes together.
Design and Engineering
Every suppressor starts in the engineering department, where SilencerCo’s research and development (R&D) team designs and prototypes new products. This group works with advanced CAD software and in-house testing equipment to validate ideas before they ever reach the shop floor.
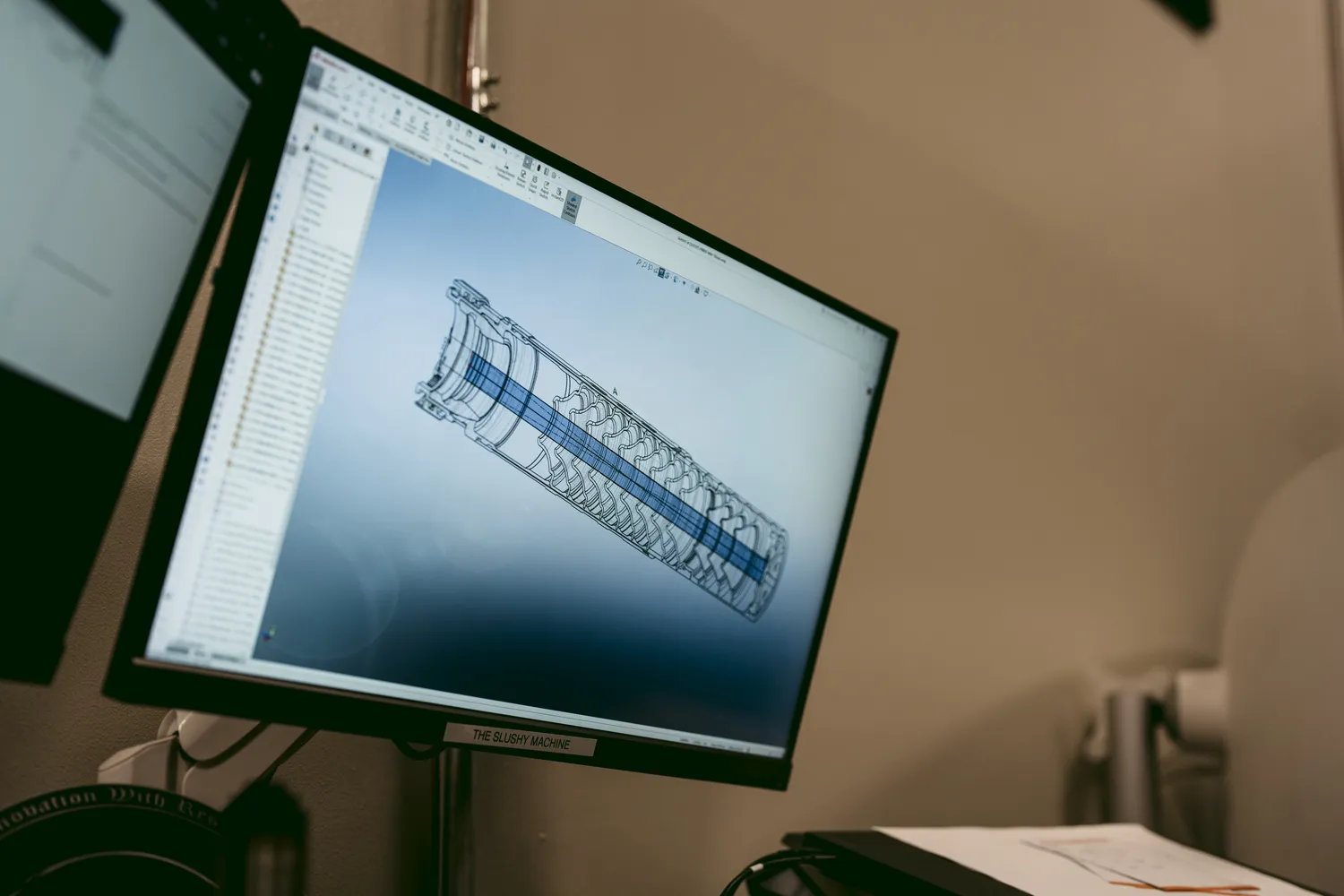
Materials
Raw materials arrive in long metal bars—aluminum, titanium, and stainless steel—that are stored on racks and matched to specific parts. Depending on what’s being manufactured, these bars are cut to precise lengths for machining.
Most machines use automatic bar feeders, which means the material needs to be cut to the correct size before loading. The use of long and short stock allows for flexibility between high-volume runs and specialty components.
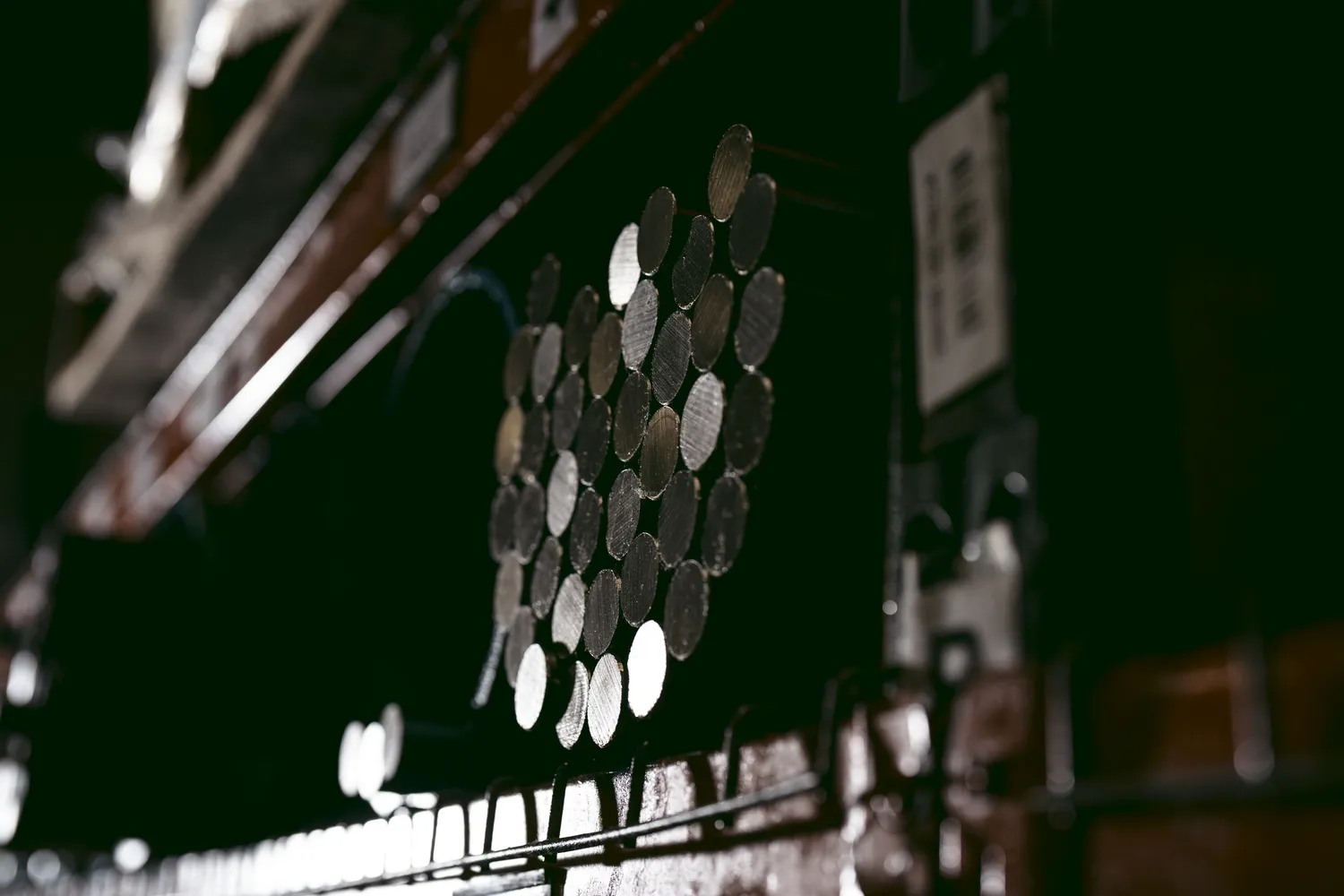
Precision Machining
SilencerCo uses a mix of vertical mills, CNC lathes, and Swiss machines to machine parts with exact tolerances.
Milling
Components that aren’t round—such as the Osprey suppressor, the Salvo 12, or the Gas Defeating Charging Handle (GDCH)—are machined on vertical mills using tombstone fixtures. These four-sided fixtures allow operators to mount multiple parts at once. The machine rotates the tombstone, performing sequential operations on each face.
This method enables high-volume production with minimal tool changes, improving both speed and repeatability.
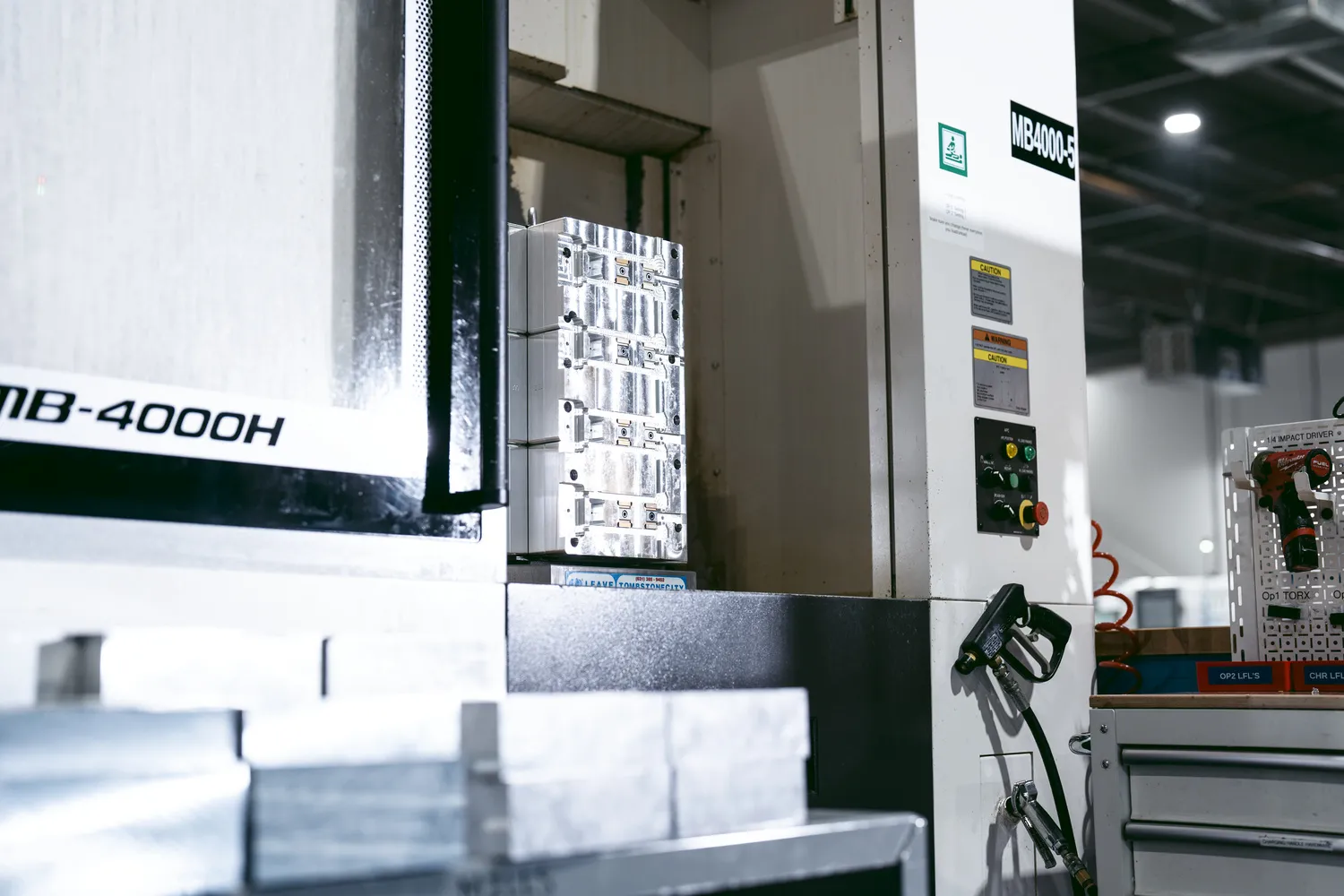
In recent years, SilencerCo upgraded to a new generation of blue machines—nicknamed “Smurfs”—which offer increased flexibility. Unlike older models that require full changeovers between runs, the Smurfs can load and recognize multiple programs at once, allowing different parts to be run back-to-back without stopping the machine.
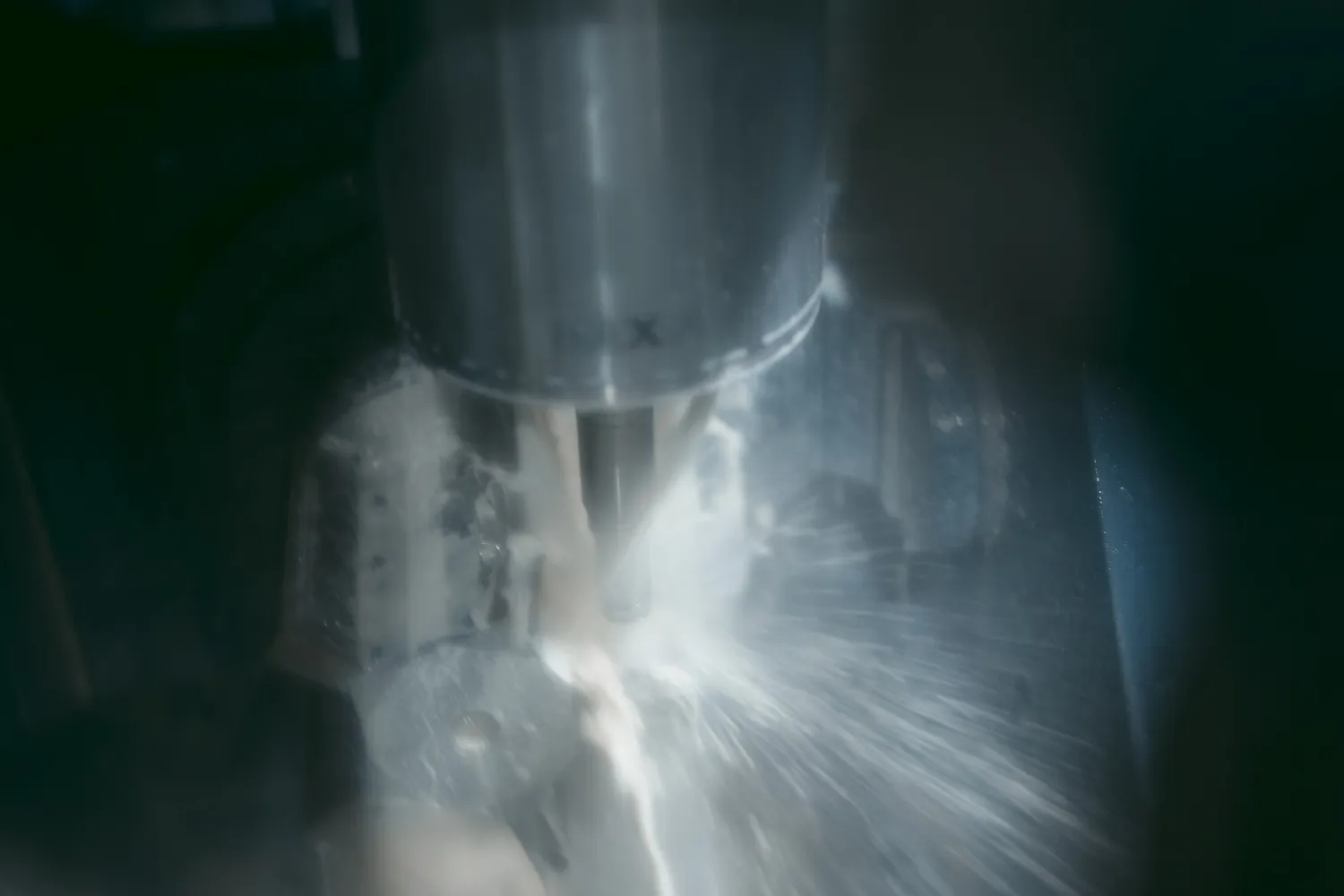
One clear example of machining precision is in the GDCH. Parts are machined in multiple passes, with the tool cutting each face, and then the part is flipped into a matching fixture to complete the second side. The video below shows the complete process, from milling to packaged GDCH.
Lathes & Swiss Machines
Round and cylindrical parts—such as suppressor tubes, thread mounts, and front caps—are machined on CNC lathes. These machines often feature a main spindle and a sub-spindle. The main spindle performs the initial cuts, then hands the part off to the sub-spindle to complete back-side operations. This enables continuous part handling with no need for manual repositioning.
For high-precision, small-diameter components like spacers or washers, SilencerCo uses Swiss-style machines. These machines use oil instead of coolant to maintain better thermal control and reduce tool wear. Their ability to machine both ends of a part simultaneously increases throughput and decreases the chance of scrap.
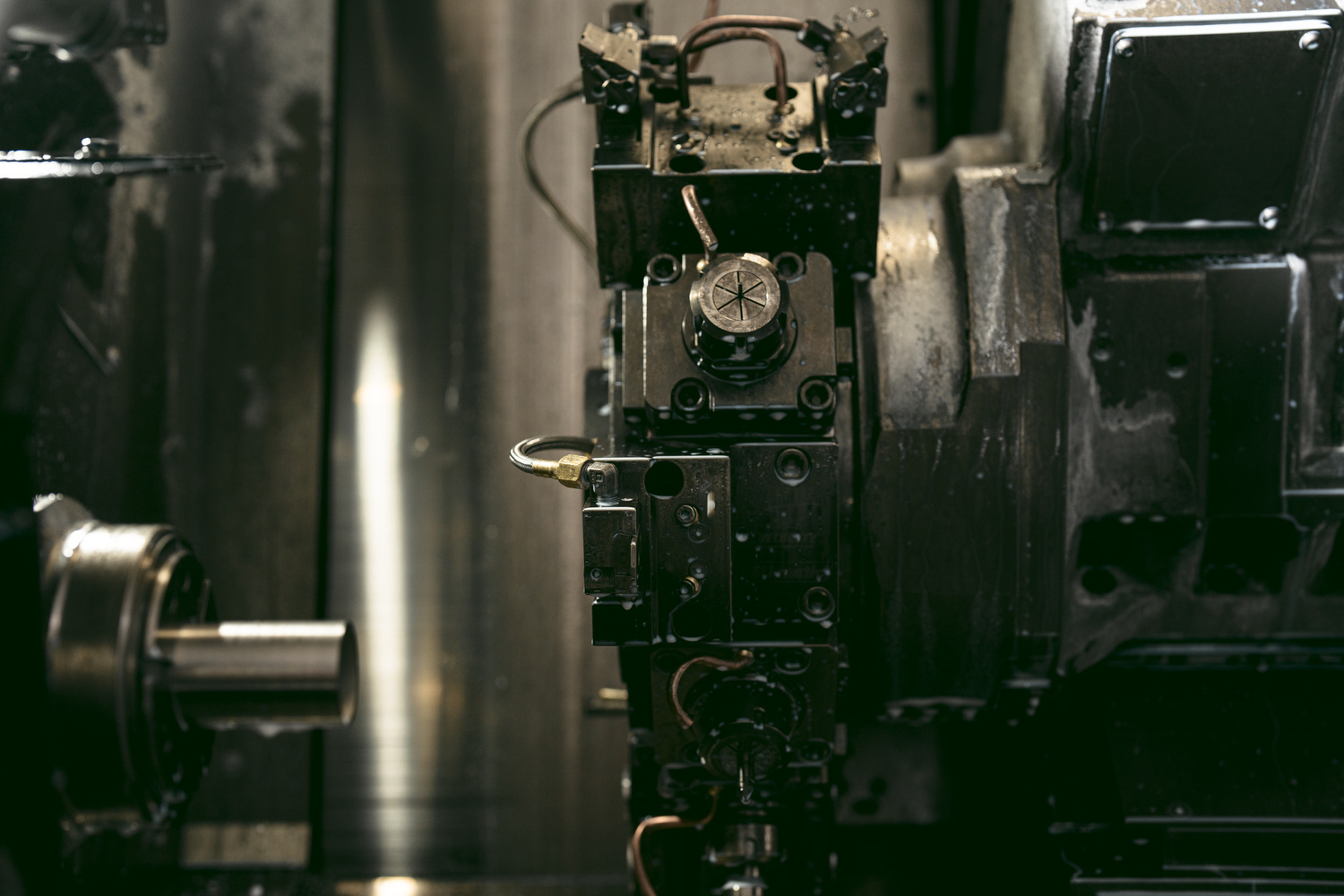
All of this work generates heat, so a coolant mix (water, soap, and oil) keeps tools and parts within safe temperature ranges. Coolant is filtered and recycled on-site for environmental and cost efficiency. Metal chips are automatically removed by high-pressure spray systems and conveyors to keep production moving without delays.
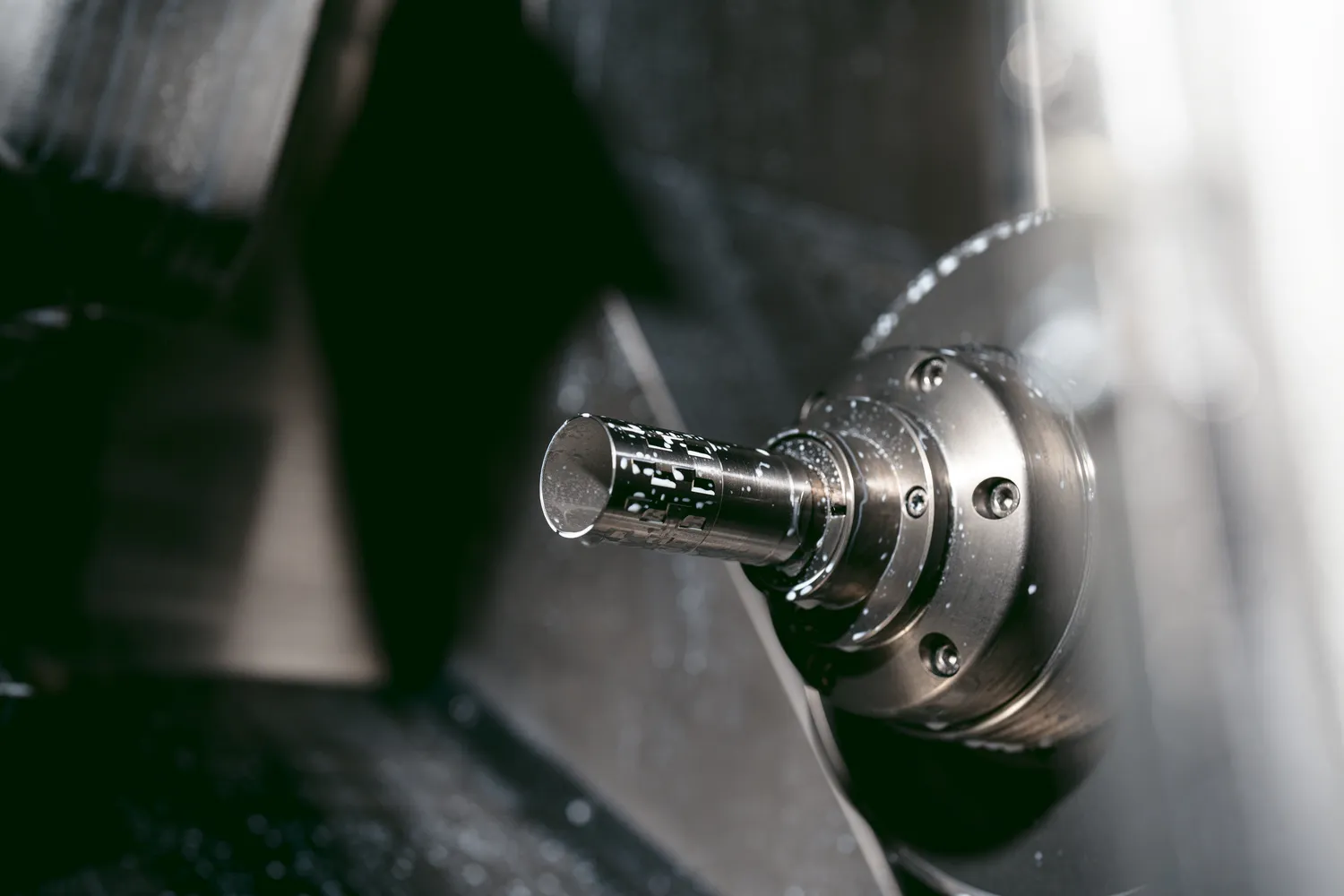
Welding and Post-Machining
After initial machining, some components go through laser welding, which permanently fuses parts together. This process is precise, but it can cause slight warping due to heat. Parts are corrected afterward and sometimes go through additional machining steps to restore critical dimensions or re-cut threads.
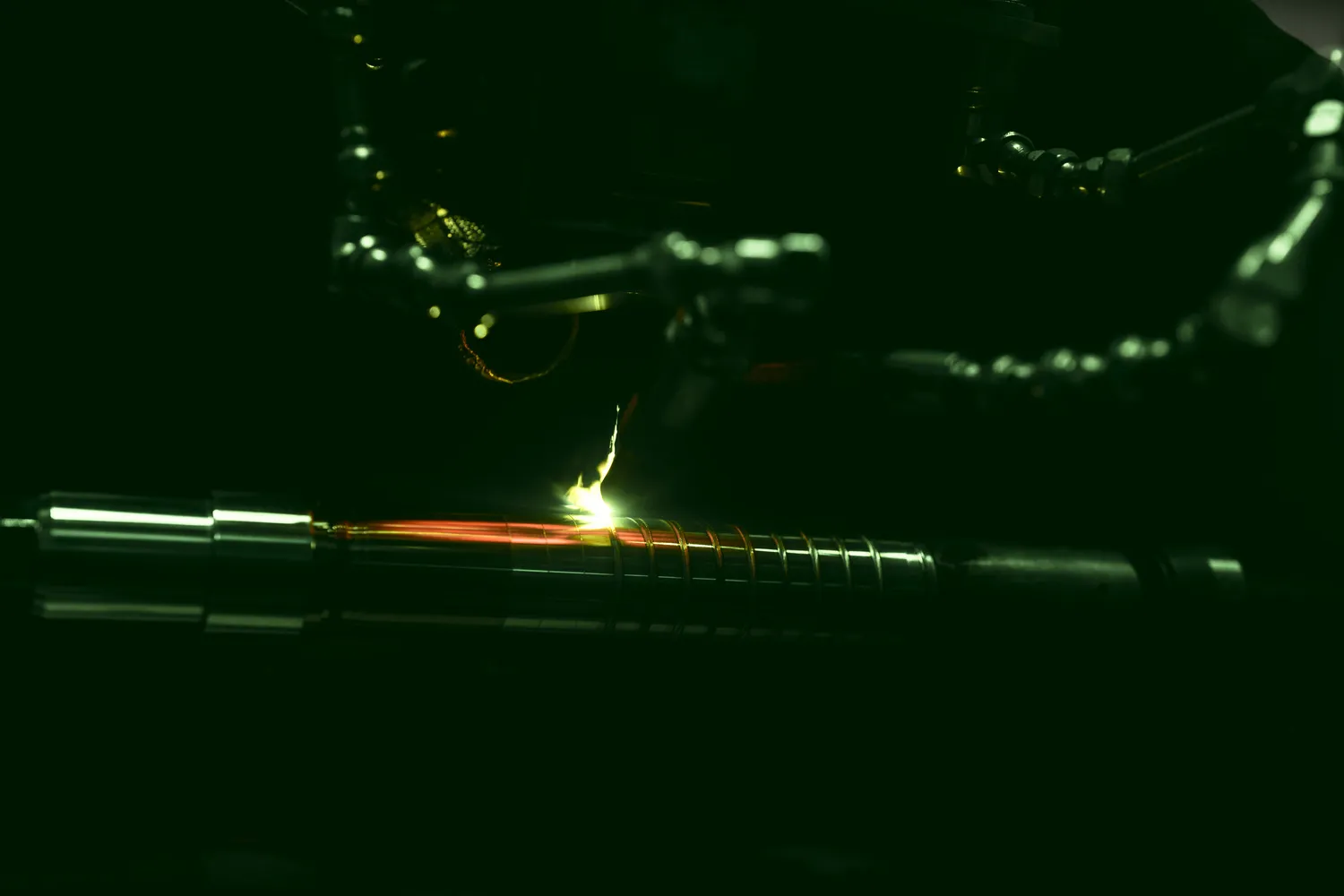
Quality control ensures that all parts meet the required specifications, whether they are being assembled directly or going through post-production processes like coating and anodizing.
Laser Engraving
Parts are sent to laser engraving stations to receive logos, model names, and serial numbers. This step isn’t just for aesthetics—it’s required for compliance with the National Firearms Act (NFA). Once a serial number is applied, that part must be tracked throughout the entire facility without exception.
SilencerCo uses automated laser systems that engrave multiple parts in one setup, allowing for consistent, high-speed marking. These engravings are clear, permanent, and traceable—critical for quality assurance and legal compliance.
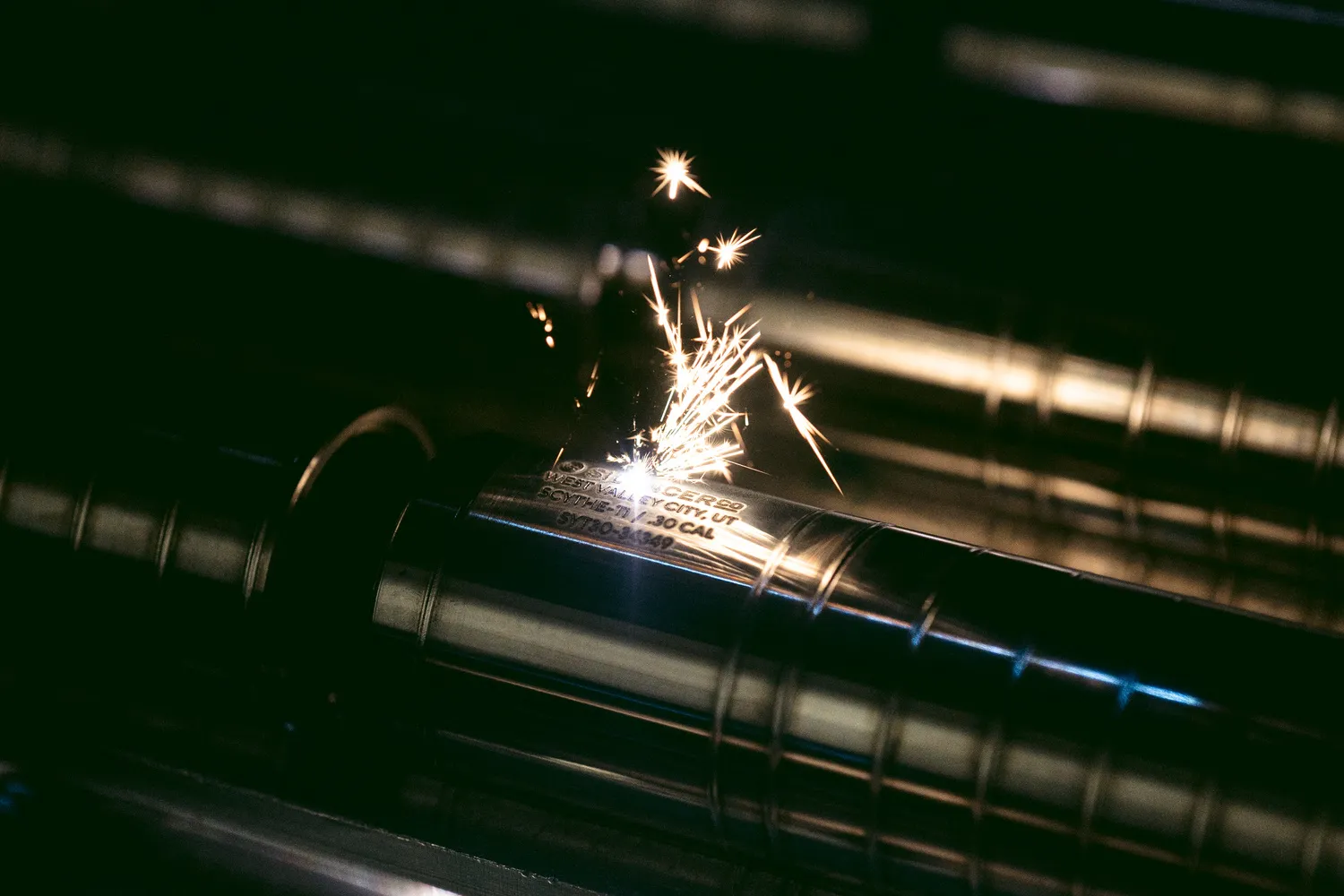
Metal Finishing: Anodizing and Coating
Once machined, welded, and enraged, suppressor components move into finishing. This includes anodizing, heat treatment, or coating—depending on the material and intended use.
Anodizing
Titanium and aluminum parts are anodized to create a protective oxide layer that hardens the surface and improves corrosion resistance. This process involves passing an electric current through a chemical bath. Type II anodizing is used for titanium, while aluminum parts typically receive a Type III treatment and are dyed black for a uniform appearance.
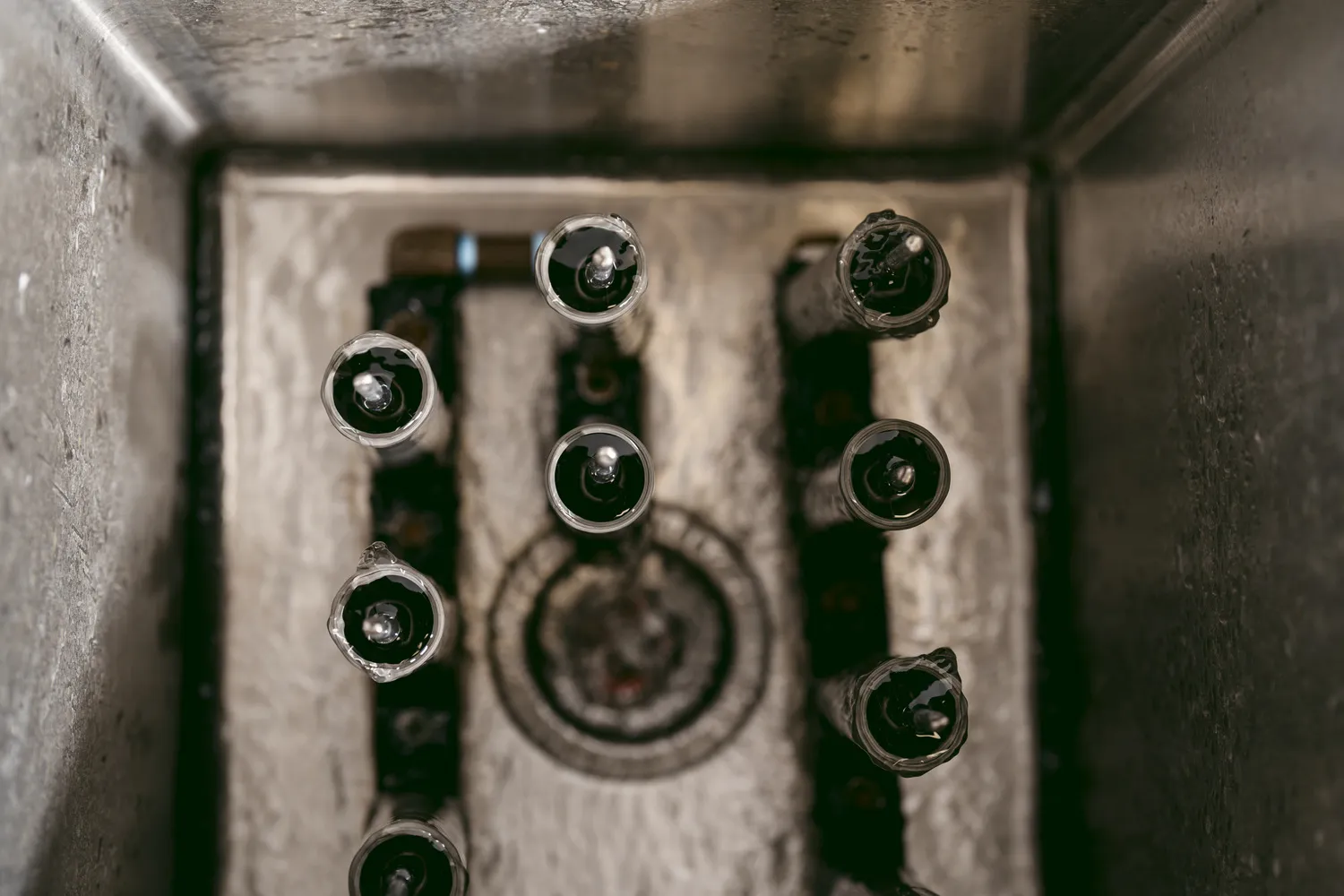
To control heat during anodizing, SilencerCo uses a glycol chiller system that cools the fluid through heat exchangers. Proper racking of parts ensures full submersion and prevents air pockets during the coating process.
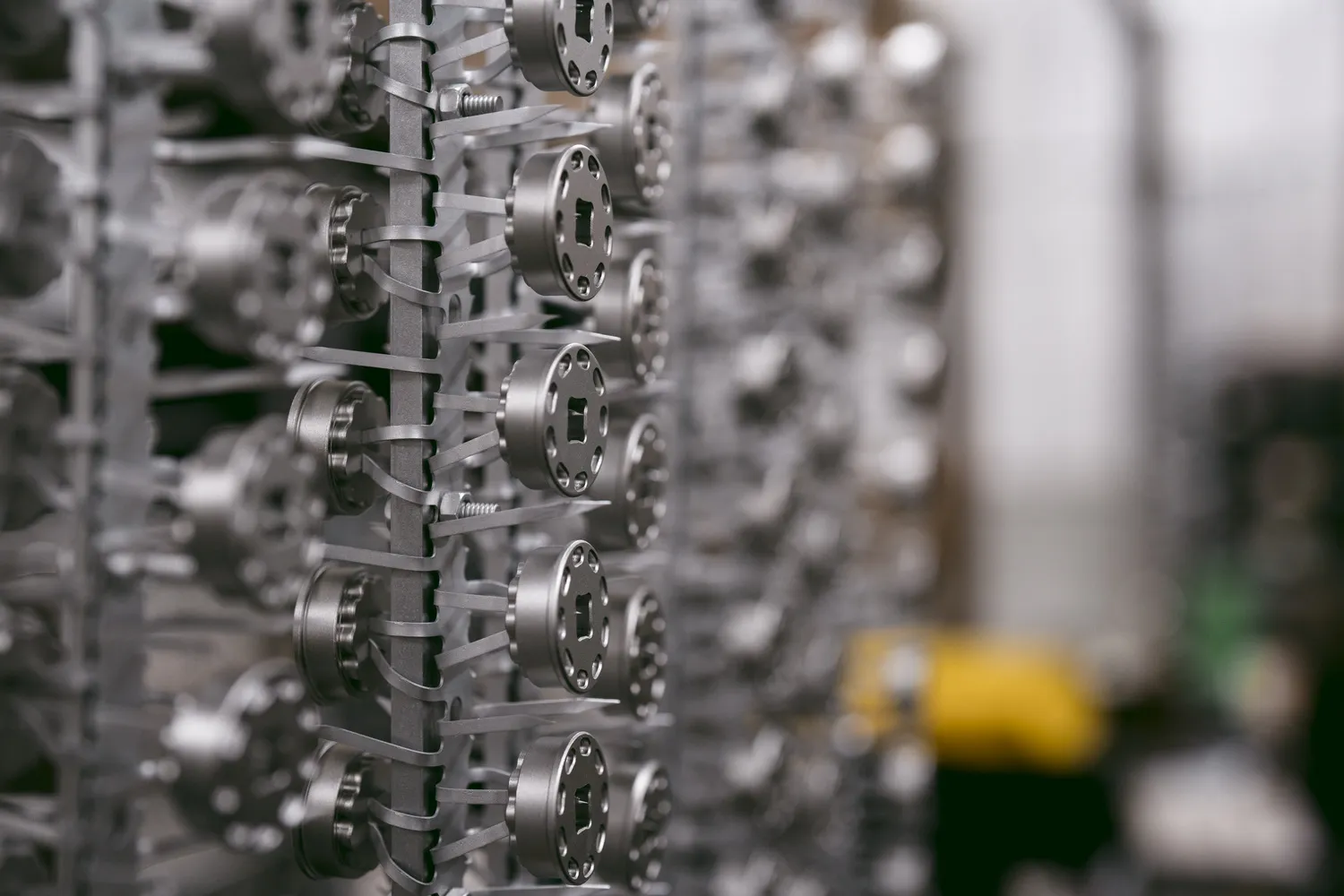
Anodizing changes the surface appearance of suppressor tubes. Before treatment, aluminum shows a raw, silvery sheen that transforms into a rich, matte black finish.
Titanium, as seen below, starts with a natural silvery-gray tone and develops a subtle, earthy matte finish after anodizing—enhancing corrosion resistance while preserving its unique character.
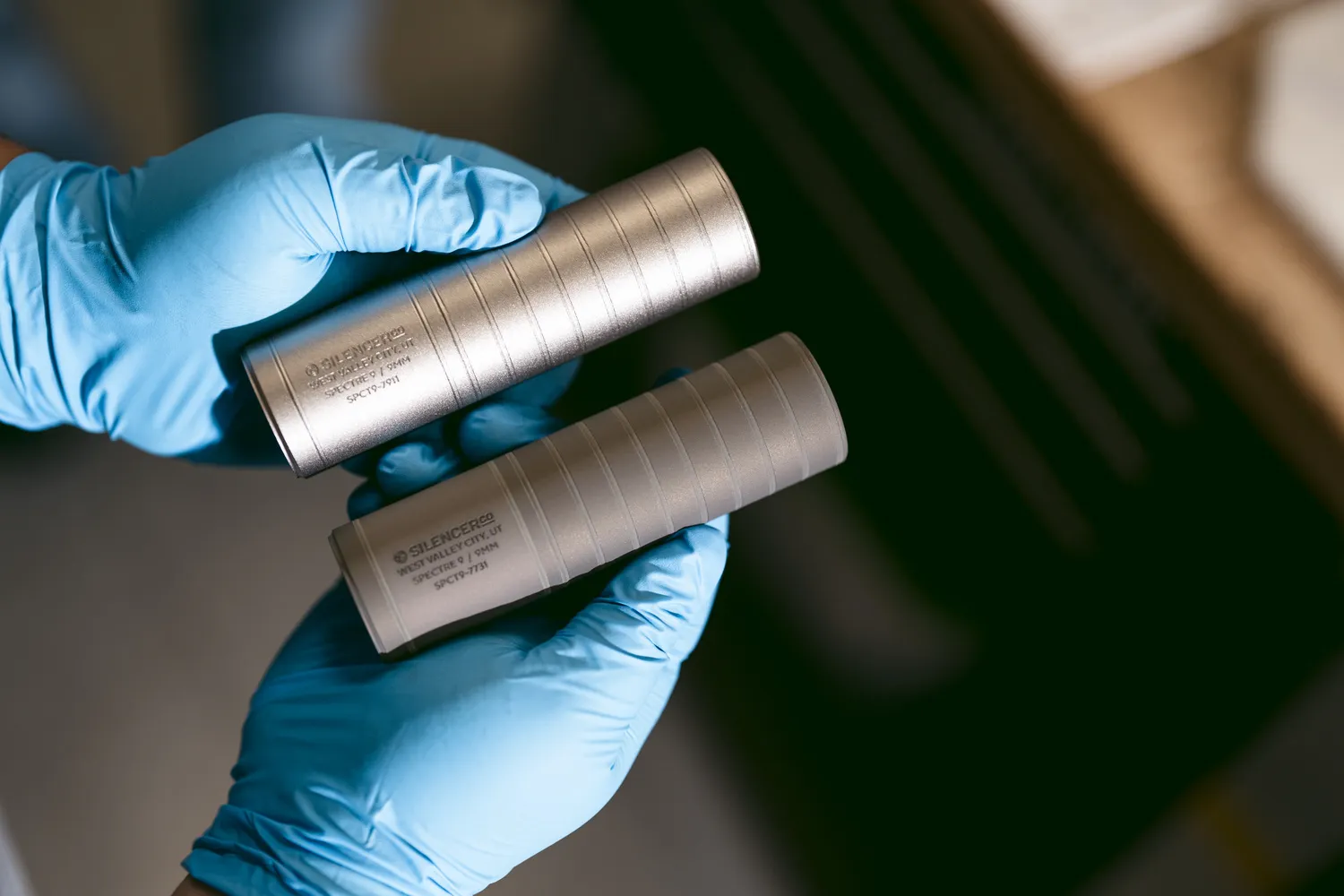
Heat Treating
Steel parts are heat treated to improve their internal structure. By heating and cooling them at specific rates, the crystalline structure of the steel aligns to increase strength and flexibility. This step is essential for components subjected to high temperatures and pressure, such as blast baffles and mounts.
Black Oxide
Black oxide is a chemical process where steel parts are immersed in a heated salt bath, causing a controlled oxidation that forms a hard, corrosion-resistant layer. This layer is actually part of the metal itself, giving a durable matte black finish that improves wear resistance without adding thickness or altering dimensions.
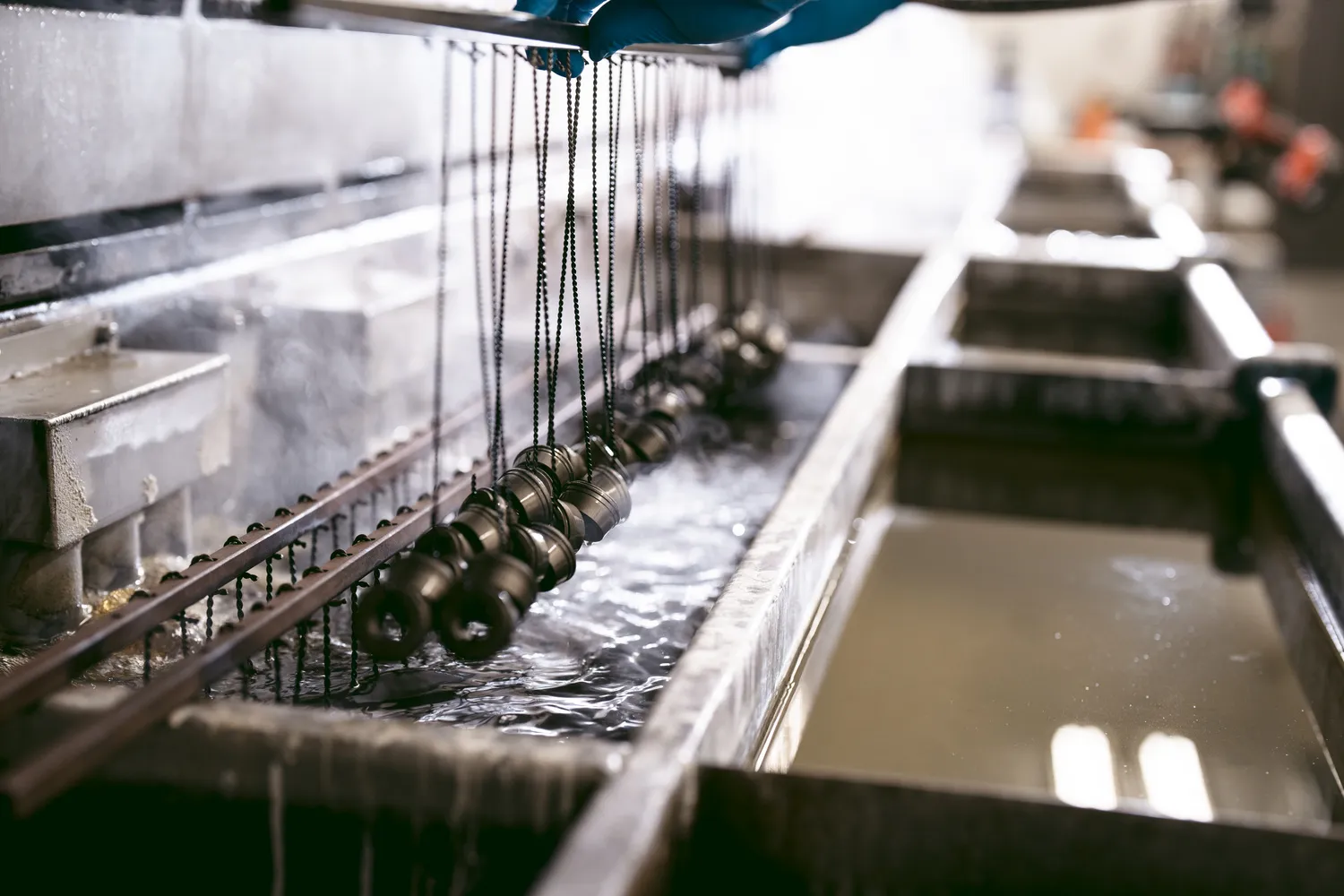
Quality Control and Testing
At every stage, SilencerCo puts a strong emphasis on quality control. Parts are inspected with calipers and other precision tools to ensure tolerances are met. Any variation from the spec is flagged and corrected before moving forward.
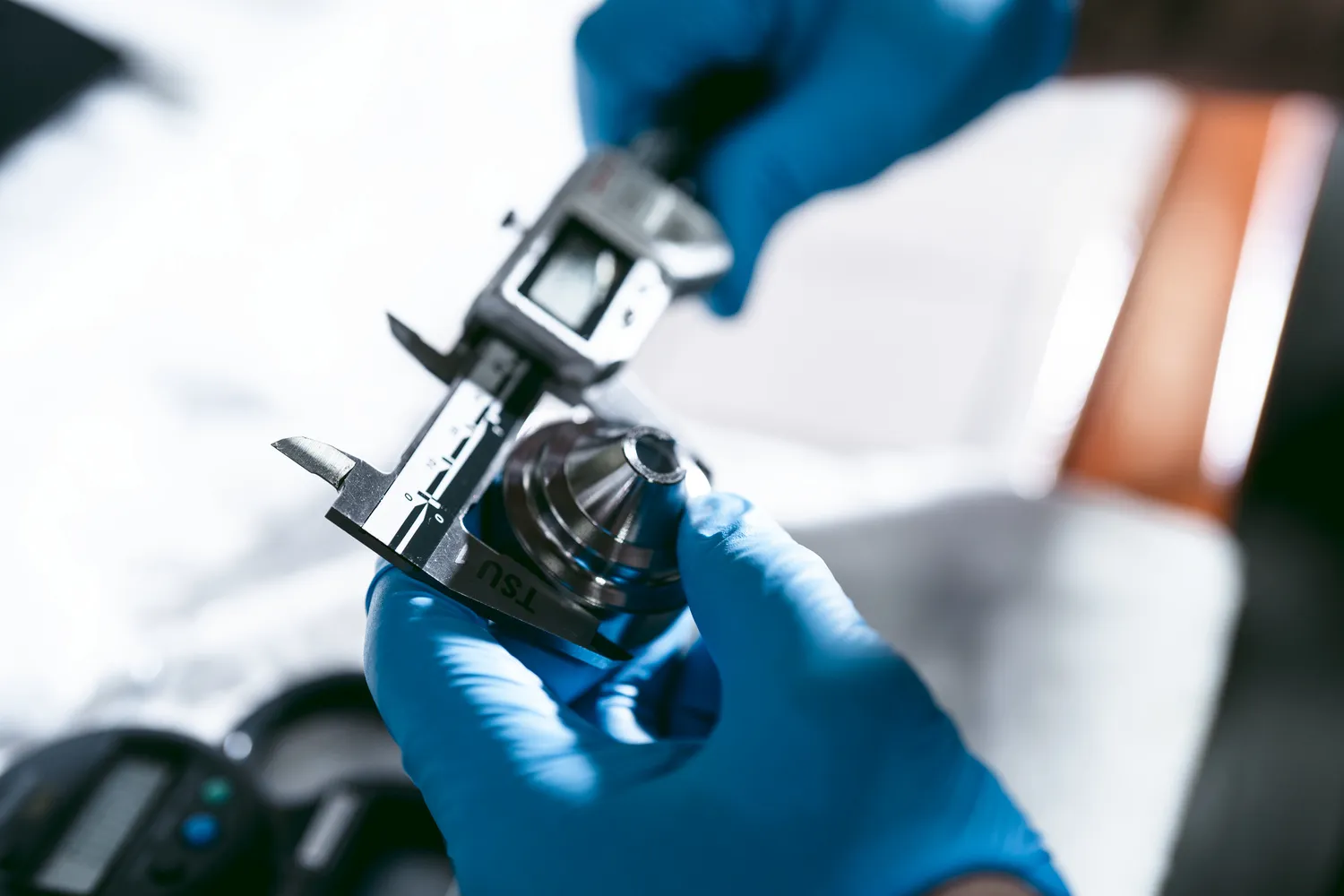
Once suppressors are fully assembled, they undergo rigorous testing—including live-fire endurance trials. SilencerCo runs thousands of rounds through suppressors each week to evaluate durability, function, and sound performance.
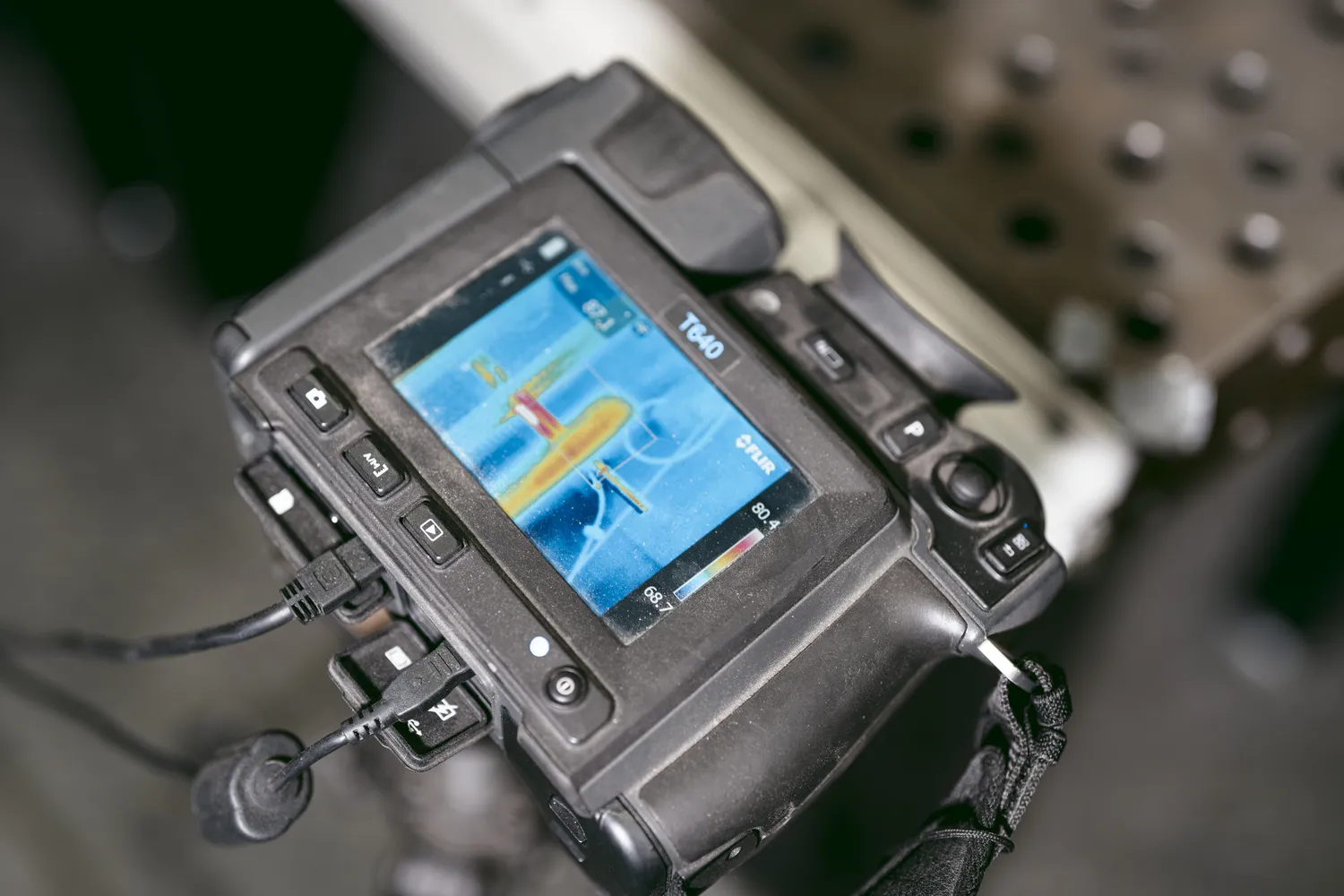
Thermal imaging (above) is one of many tools SilencerCo uses to verify how suppressors handle heat during sustained fire. Likewise, weld strength is tested using high-pressure impulse tests inside a secure housing—the ‘Boom Box’—simulating the kind of stress these products might face in real-world use.
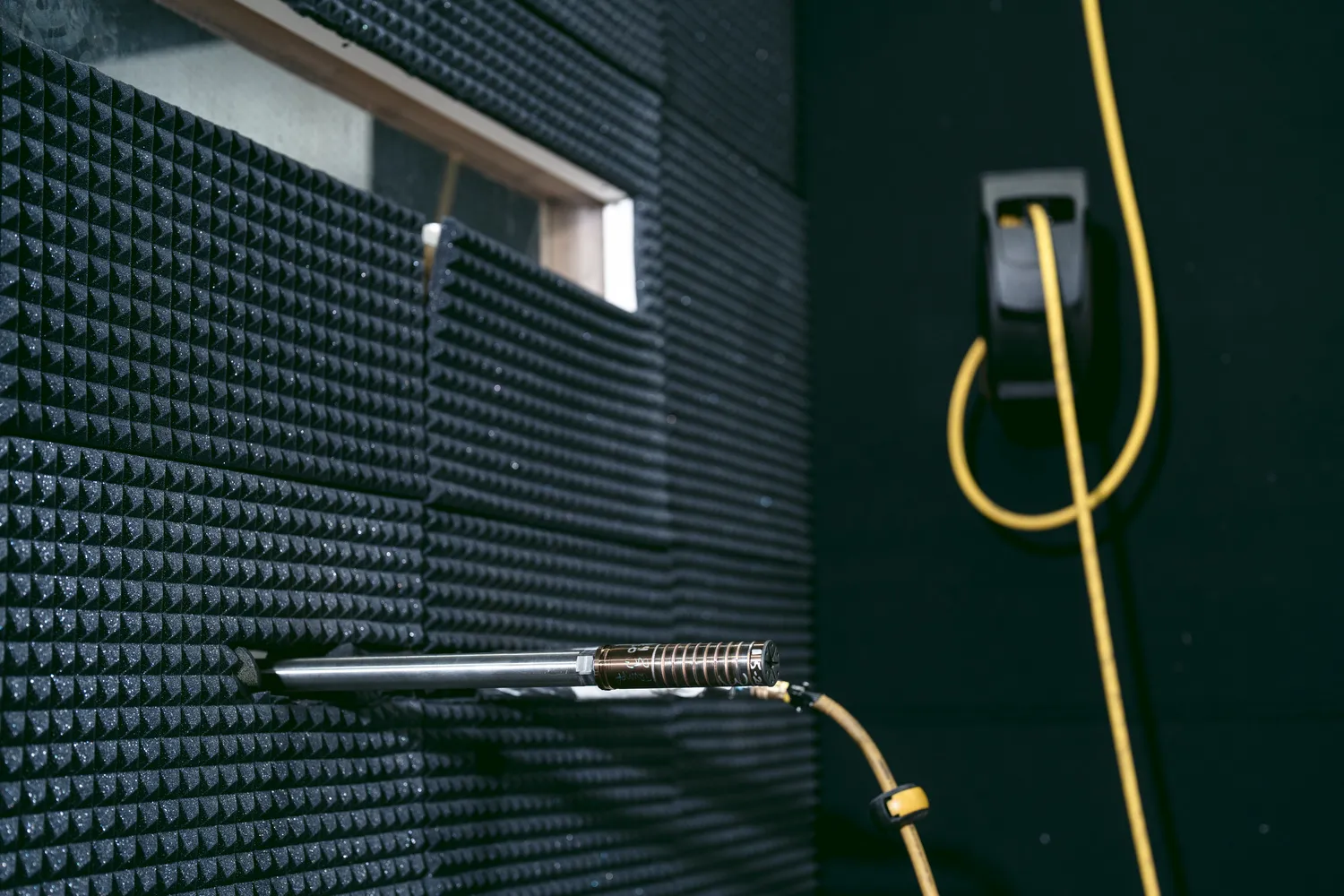
This deep commitment to quality is what allows SilencerCo to offer its renowned lifetime warranty. If a suppressor ever fails due to a manufacturing defect, SilencerCo stands behind it with prompt repair or replacement. The company’s internal warranty evaluation process ensures each claim is handled with the same level of care that goes into manufacturing.
As Jonathon Shults, founder and president of SilencerCo, puts it, “It’s putting that customer experience first. I want people to feel like they’re part of our family. If something’s not right, we’re going to fix it fast. That’s why we build quality in from the start.”
Packaging and Shipping
Each unit follows a specific assembly checklist to ensure consistency and compliance. Parts are torqued, sealed, and aligned according to engineering specifications. Once built, suppressors are boxed with their serial number clearly visible on top, making it easy for dealers and customers to verify what they’ve received.
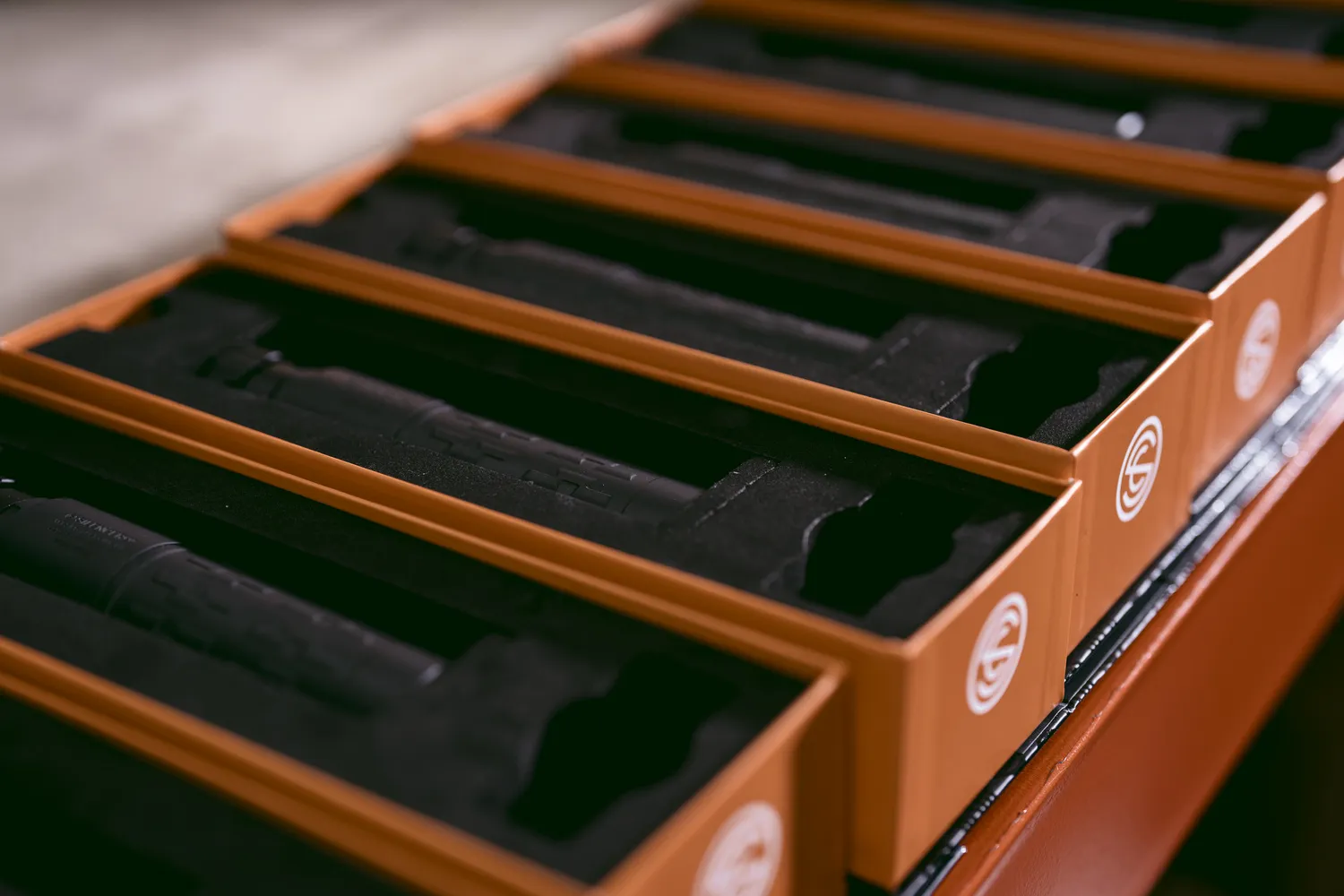
Packaging stations are organized to allow the team to assemble, inspect, and pack a complete suppressor in one seamless process. This efficiency ensures that serialized items are handled with precision from start to finish..

Conclusion: Precision at Every Step
The process of making a suppressor isn’t just about threading a tube onto a barrel and calling it a day—it’s a complex orchestration of materials, machines, and skilled craftsmanship. At SilencerCo, each suppressor is the result of dozens of carefully controlled steps, from material selection and advanced machining to finishing, testing, and final assembly.
By keeping nearly every part of the process in-house, SilencerCo maintains strict control over quality and ensures each suppressor meets the high expectations of its users. Whether it’s a first-time buyer looking for their initial rimfire can or a professional relying on a suppressor for duty use, every customer receives a product built with care, precision, and pride.
In a market where shortcuts can compromise reliability, SilencerCo’s methodical approach sets a high standard—and proves that American manufacturing, done right, means confidence you can carry forward.