Home / Silencer & Gun News / SilencerCo Plant Tour: The Magic Behind Suppressors
SilencerCo Plant Tour: The Magic Behind Suppressors
SilencerCo Plant Tour: The Magic Behind The Scenes
Jason Baird
Have you wondered what sort of “magic” happens that causes metal tubes to become suppressors? I have, so recently when invited to go on a SilencerCo plant tour at its headquarters in West Valley City, Utah, I jumped at the chance to do something that few are allowed to do. Hopefully, my record of the experience will help demystify the suppressor manufacturing process. Maybe it will also give you an understanding of the processes involved in turning tubing, sheet stock and other raw materials into those finely-fitted and highly regulated cool devices we know as SilencerCo suppressors.
While onsite, I was able to witness the workmanship and materials involved, as well as the design, engineering, and machinery required to manufacture silencers. Best of all, though, I met some of the people who actually make the silencers – those folks who genuinely take pride in producing some of the bestselling suppressors on the market.
The pictures accompanying this article document some of those people, the machines, and materials. I did not photograph in detail some parts of the facility or the processes for proprietary and intellectual property reasons, but my tour guide, Josh Dietz (the Press Relations Manager at SilencerCo), politely allowed me to take enough pictures to illustrate the behind-the-scenes work that goes into producing suppressors, accessories like ASR muzzle devices (MSRP $92), AR lower receivers (MSRP $249) and the integrally suppressed Maxim 9 pistol (MSRP $1499).
The Engineers
During the day of my plant tour, Josh and I visited the engineers of SilencerCo’s Research and Developement team, where he introduced me and started a lively discussion of the company’s current and future products. The engineers have varied backgrounds and wide ranges of expertise, but all seem to have one thing in common – they really enjoy designing, testing, and using suppressors and suppressed firearms. We visited the underground armory and testing range, where I saw and handled many of the different firearms the engineers keep on-hand for checking the fit and function of suppressors. The engineers also showed me the chronographs and high-speed video equipment they use to analyze the effects suppressors have on their host firearms (I recognized several systems from my missile, blast and explosives testing background, also known as “high speed/low drag” systems).
SilencerCo Plant Tour
After retrieving the PPE (safety glasses and earplugs) required to be worn on the manufacturing floor of the facility, Josh and I started our tour in the materials receiving area. Using horizontal band saws, an employee cut metal tubing and bar stock from large bundles into proper lengths for feedstock to be fed into automated machinery.
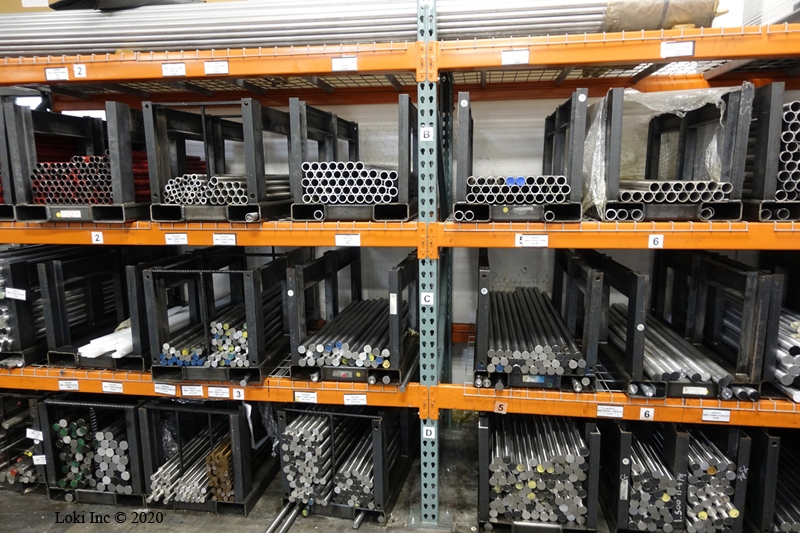
Later, I saw some of those bars set-up to feed into CNC horizontal turning centers (CNC is the acronym for Computer Numerical Control, and a CNC turning center is a computerized lathe that can usually also do milling operations) elsewhere on the floor.
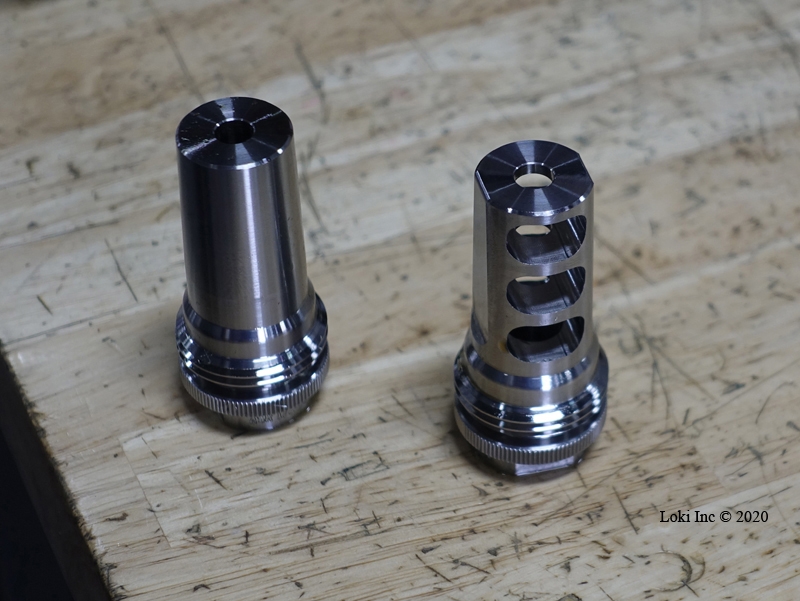
A team of workers monitored the CNC milling and cutting processes, adding the human touch where necessary.
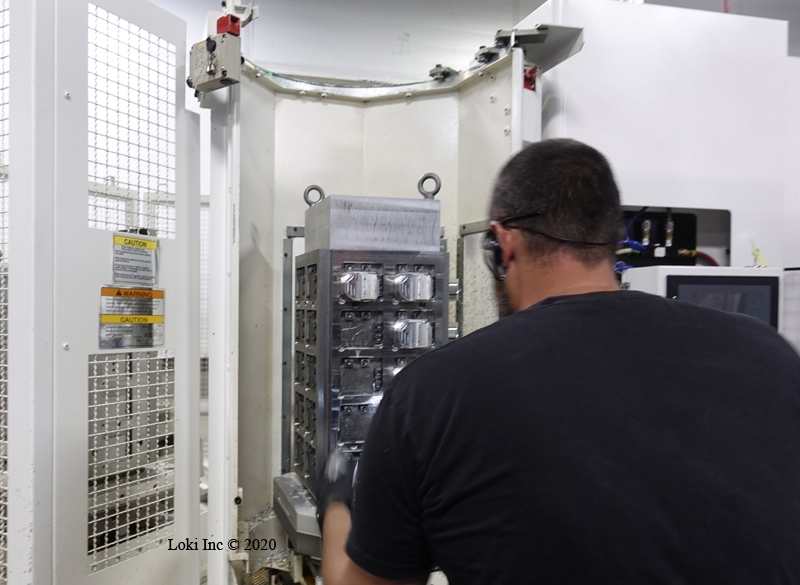
One machine cuts aluminum stock into one of the newer SilencerCo products – the SCO15 AR lower receiver.
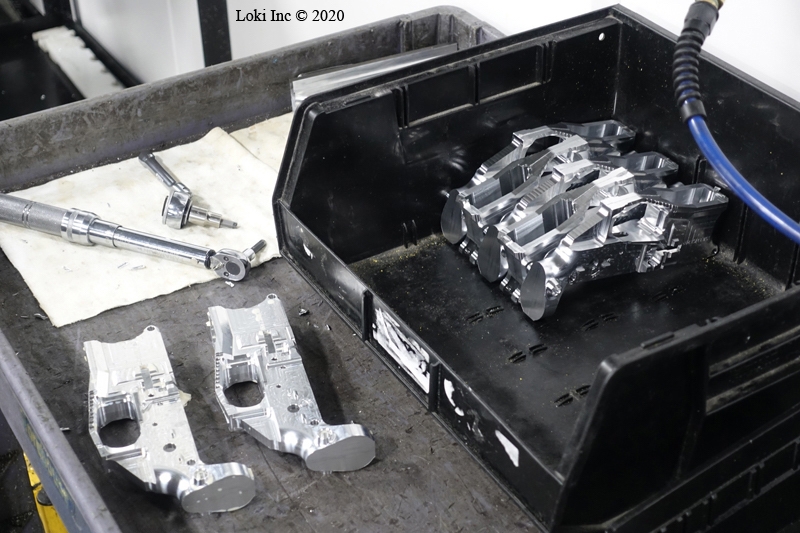
Some of SilencerCo’s cans can be disassembled for cleaning. The cans the company didn’t design for disassembly, however, are typically welded together. It is likely that fewer parts are rejected due to defects.
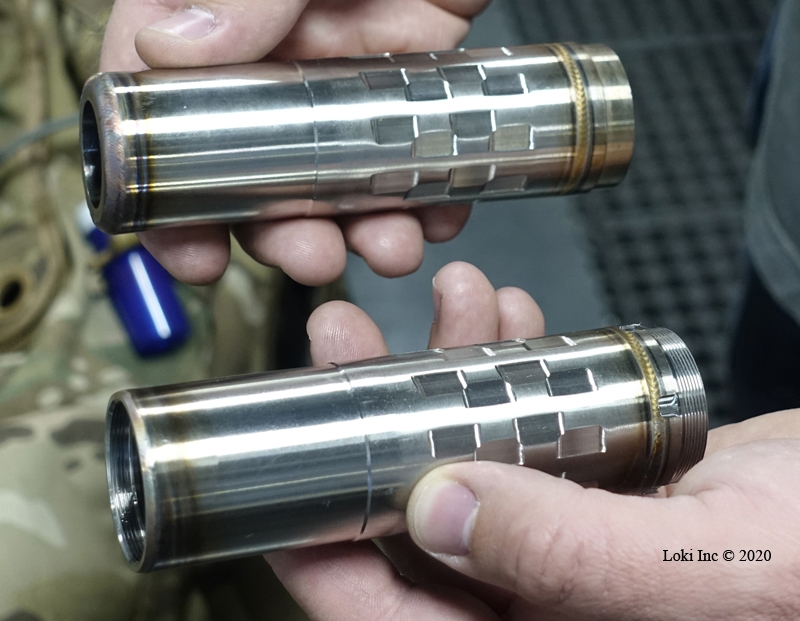
SilencerCo does most of its suppressor surface treatments, such as black oxide coating and metals anodizing, in-house.
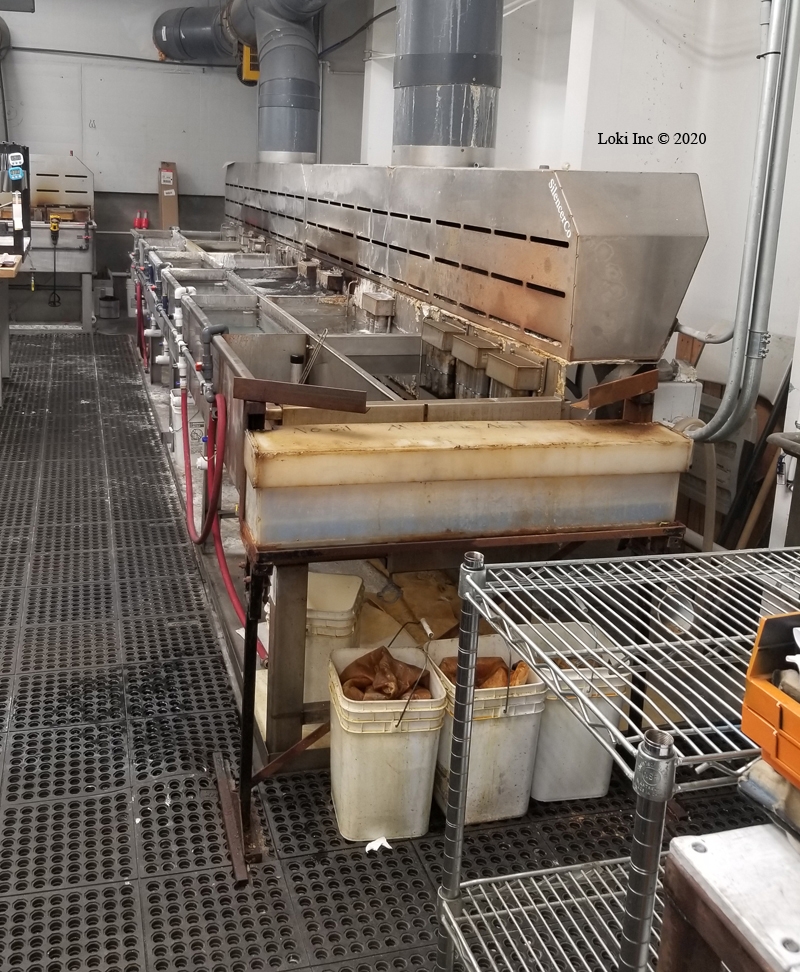
Since the company does the whole manufacturing process, from raw materials receiving to packing and shipping the finished accessories and suppressors, it offers several areas where employees work inspecting products, cleaning them and packing them for shipment.
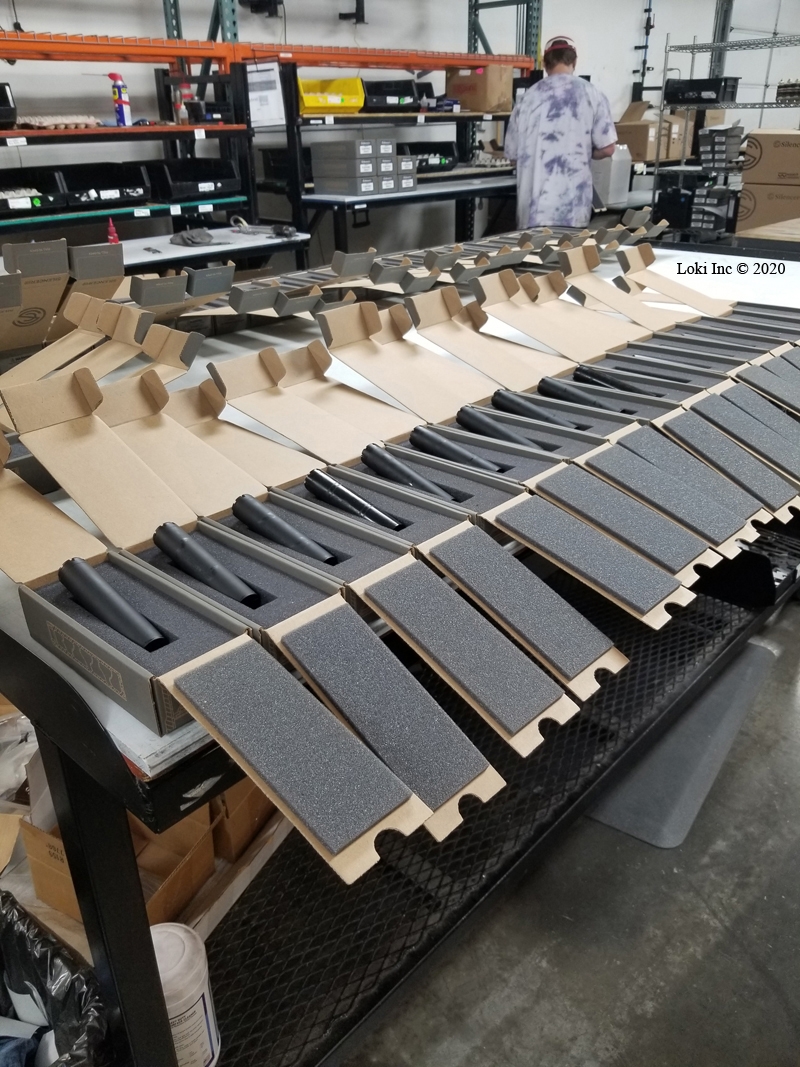
SilencerCo Plant Tour: Seeing the Maxim 9
In one area of the plant, I came upon racks of the Maxim 9, the integrally suppressed 9mm pistol, waiting for proof testing in-house.
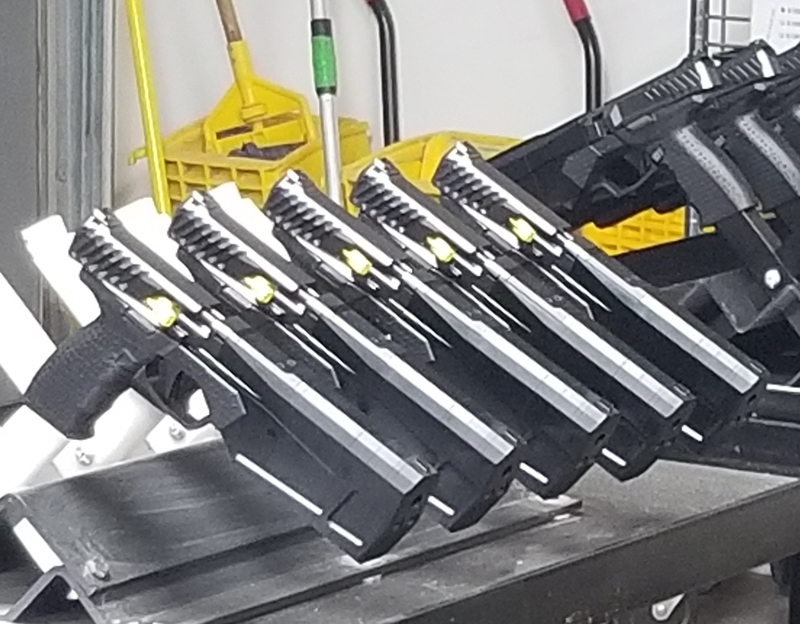
SilencerCo designed and built the Maxim 9, said to be the world’s first of its type that can be easily holstered and is hearing safe with all varieties of 9mm ammo. Fortunately, I previously fired the gun and talked, during my tour, with the SilencerCo engineer that designed it.
The pistol is not svelte, and at first, appears ungainly to handle and control because of the necessity for gas expansion and baffling chambers at its front end. Appearances are deceiving, however, as it handles well and the action offers the typical feel of a 9mm pistol during recoil – except, of course, for the noise! The gun is hearing safe outdoors in its long version, even with supersonic ammo, and that can be a big advantage in many situations.
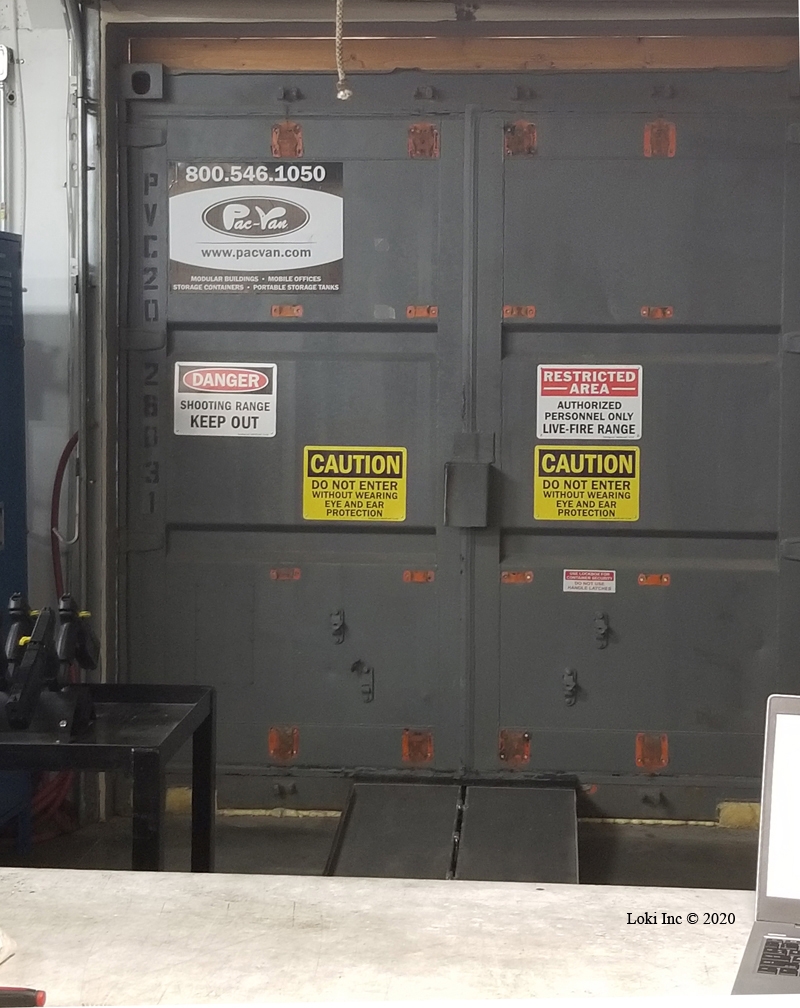
Overall, I really enjoyed the SilencerCo plant tour and being able to see and hear what goes on in the making of the many suppressors, accessories and the Maxim 9 pistol. Speaking with several of the workers about their jobs, and their roles in the design and making of these interesting products, gave me insight into the ethos of SilencerCo. It also gave me a better appreciation of their company. I hope my brief description has helped you, too.